Frutex has been stocktaking smoothly with Sapphire WebPack
June 26, 2020 11:06 am | by John Adams
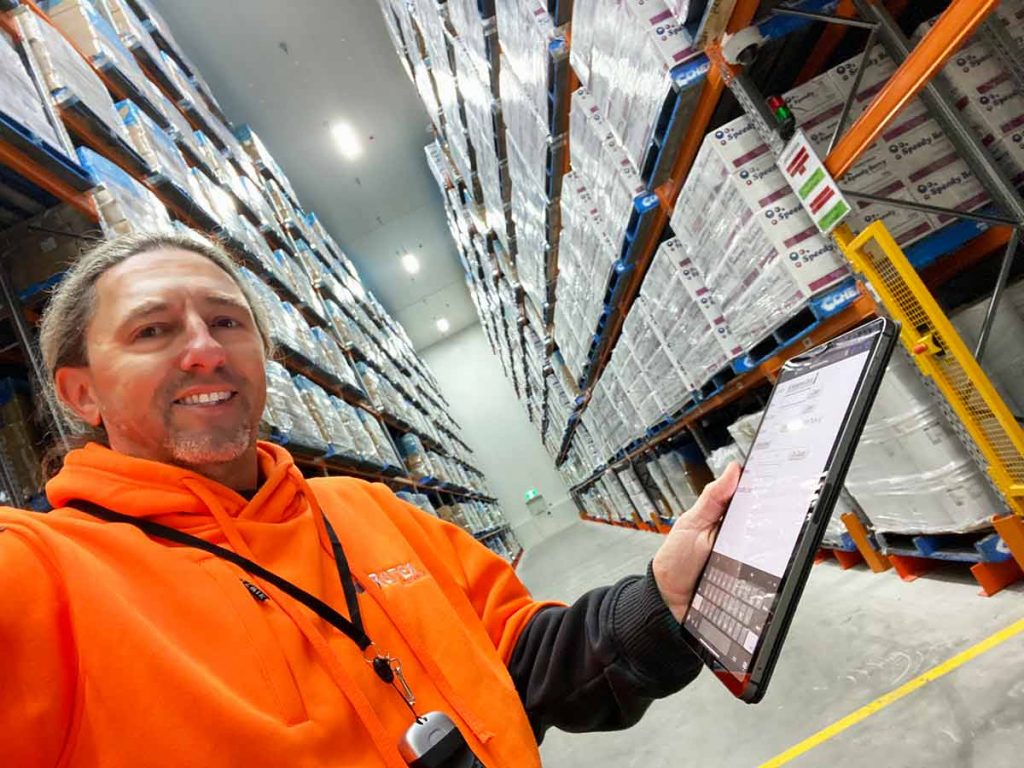
Frutex's Frozen Stocktake section (-20℃)
Frutex, who has been a client with us since 1999 is currently getting ready for EOFY. Their site entails 60,000 square metres with total of seven warehouses. The company is a technology leader in the food industry, investing heavily in state-of-the-art plants and equipment.
Harry, who is the IT & Marketing manager of Frutex, says:
“Heads up, we are stocktaking today using SapphireOne’s new improved multi-warehouse support, with live stocktake visual map updates, which shows us what’s been counted as we go along…. it’s been great working with the SapphireOne team who have worked tirelessly over the last couple of weeks to make this possible for us.
We recently built a new warehouse / freezer / production facility that adds over 12,000 pallet spaces to our warehousing that is now a total of 44,000 pallets of dry and frozen storage.
Using Sapphire’s WebPack we are able to stocktake the entire facility in 2 days, with 15 teams of stocktakers working simultaneously on iPads, we also have recently installed a new 10G ubiquity network utilising over 100 UniFi devices with 100% site Wi-Fi coverage and over 100 surveillance cameras monitoring the site. The entire operation is easily managed by a very small IT team and monitored via iPad and iPhone apps.”
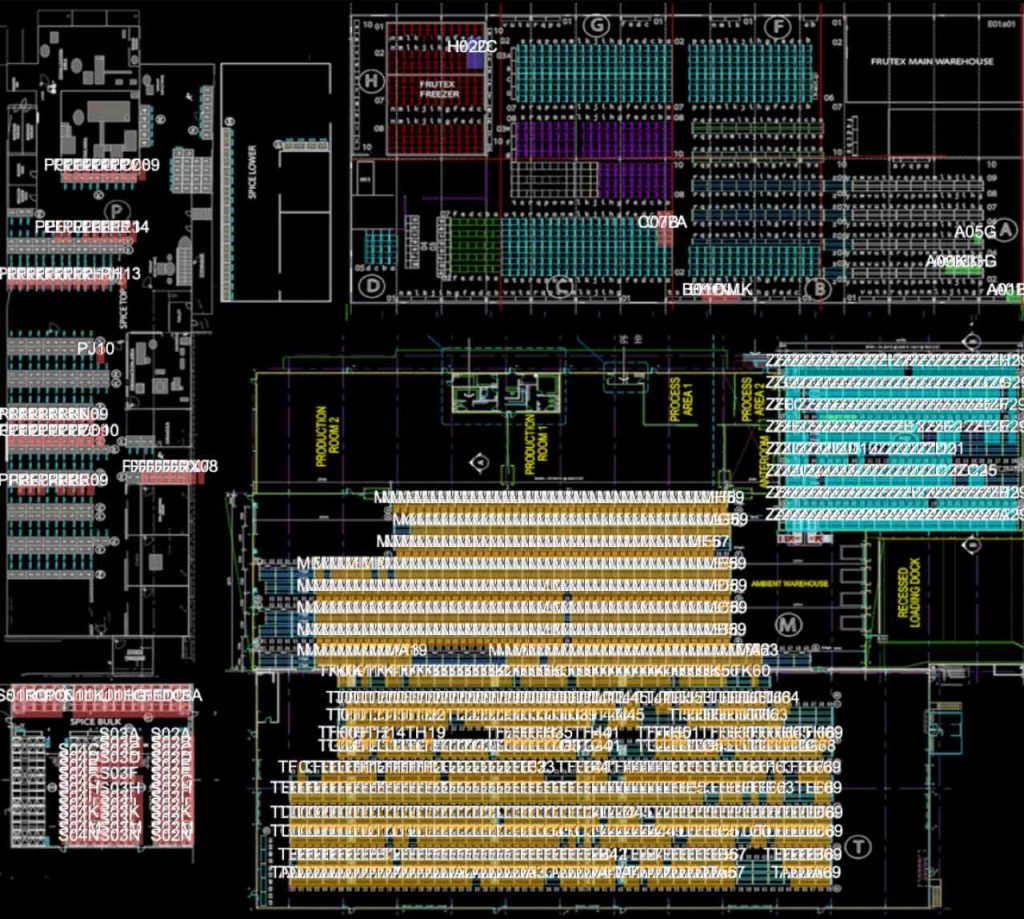
Frutex is a user of the Sapphire custom Web Pack, which is fully integrated into all company warehouses and offers warehouse mapping as a functionality. This allows all stock to be tracked and viewed live on portable iOS devices over a company’s Wi-Fi. Their stocktaking incorporates a total of nine locations.
For more information about all the benefits of SapphireOne’s integrated ERP, CRM, DMS and Accounting Software solution, sign up for a live demo with us. Here you can also read more testimonials from our long-standing clients.
Warehouse API + SapphireOne = Flow… The journey of a thousand miles begins with a single step.
December 3, 2019 8:40 am | by John Adams
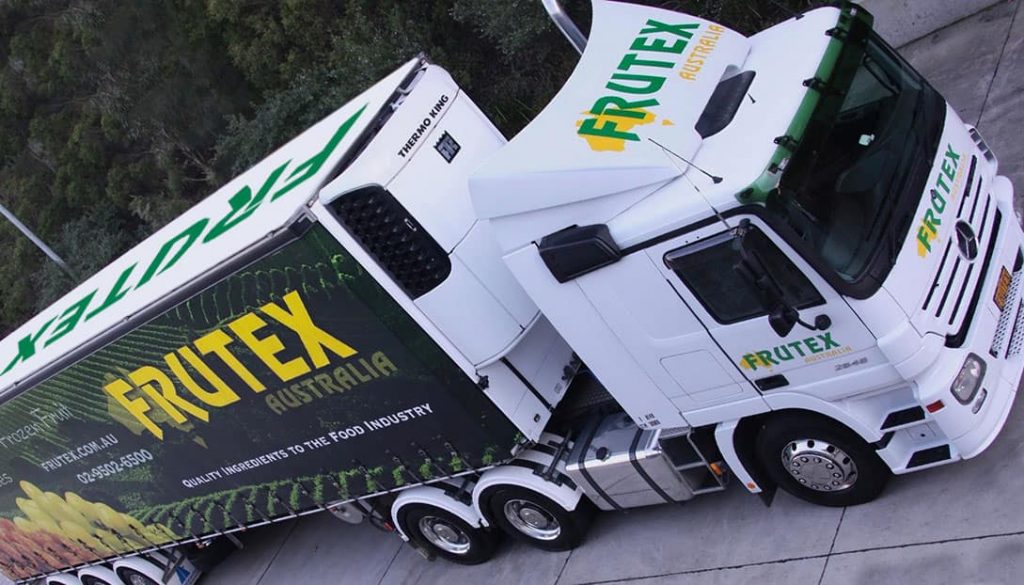
With SapphireOne’s highly customisable warehouse API you can generate Customer Growth and Innovation, where all clients who have access to your API browser can connect with you in real-time and their customer journey maps.
Advantages of Warehouse API
360 Degree Analysis
Viewing your data real-time, anytime, anywhere! Run your SapphireOne simultaneously on desktop/mobile clients, and on the web.
Built for Performance
leverage the power of today’s hardware -Server technology that can handle millions of transactions simultaneously. Take advantage of an ultra-fast database to support hundreds of desktop users and millions of web and mobile users.
SapphireOne Warehouse API Integration for Frutex Australia
Implementation of warehouse API has carried fabulous success to our clients. With the integration of warehouse API, now our clients can spontaneously incorporate SapphireOne with their websites.
Harry Magiros from Frutex has explained, what would be the thing that has made the single biggest difference in their business and the Custom WebPack.
“Frutex have been running the Custom WebPack now for almost 10 years.
The biggest impact on the business is the sales reps using the Web ordering, that fundamentally changed our turnaround time and accuracy of orders coming into the business. So we’re able to take what the sales people were doing originally, or turn that into an electronic form that gave them data accuracy, more information at their fingertips and made those orders available to our internal staff to then process and get the orders picked and on the trucks, effectively 24 hours earlier than what would normally of happened. So with minimal staff, we’re able to process a lot more orders, a lot faster and more magnitude.
Where it would have taken 48 hours to turn an order around, we are doing it in under 24 hours now. And it also spread the onus from the data entry girls double entering and double handling data to the salespeople. And now that will flow on to the same interface being with customers directly with the client web portal, which is the same interface again, removing the onus from us and putting it back on the customers to get the data entry correct of what they’ve ordered. The customers can then produce a PDF or an electronic copy for themselves.
I’m hoping that clients, especially small businesses that don’t have time to do it during office hours, can sit at home while they’re having a coffee or whatever and enter their orders. So we receive the orders now at the beginning of the day and then the next day they are ready to go to our clients! They can just get put their orders in. And it’s done so on a business sense that made the biggest difference to us.
Personally, my favourite feature is the inventory locator, which is my warehouse mapping management side of it. That gives me visibility on where my stock is and allows all my warehouse staff to maintain locations of where the inventory is supposed to be within the warehouse. And again, the efficiencies we gain from that and the accuracy and the reporting, because everything that we do goes through so many certification processes and to know where your stock is and be able to find it. It’s very crucial.
In terms of warehouse staff finding product, our picking invoices give them a code of where they’re going to go to find the products. While we’re moving product around, when they’re looking for product, they just put in the product code and up comes a map and you get a translucently highlighted section on the map that shows you all the locations of the code that they have put in across seven of our warehouses, all different locations on the site.
So we don’t have to put the same product in the same bin or shelf every day. It really doesn’t matter because as long as you barcode it in or out.. you can put it wherever they want because the map is going to show them where it is so they can order an incoming stock. They tell it where it goes. you can see where it has been and where it’s going to be. Our picking areas always have consistent locations where everything goes. The bulk storage varies depending on what’s coming and what’s going, but it is in a designated general area and we can then scan the location and it tells us what is in that location or what is supposed to be in that location.
It makes Rolling Stocktakes possible, which were not possible before. Now I can say for instance today I was looking at sultanas, sultanas in the warehouse are spread over maybe 70 different locations. I can go and check every single one of those 70 locations and do it in one day with one person. In the old days when you would have to find the 70 locations, you used to basically relying on people’s knowledge and your end of year Stocktakes on telling you where things were located.
There was a place in SapphireOne where stock location was supposed to be. That was before we had this interface, there was no way of really managing it and updating it. And then the verification was like a physical map saying, that’s where you stuck it.. yes looks like that okay.. that’s where I’m standing. That’s huge, So that’s giving you real-time stock that you can do random rolling stocktake whenever you want now and you can do it pretty well instantaneously.
There are more things I like about this interface, other things like the reporting. It’s made a huge difference to be able to get my management reporting, to be able to see what my margins are doing, whether it’s client based, location based, groups, clients. Looking at my vendors stock reports is fantastic because now I can see what we used per month, per quarter, per year, per product, you can see the seasonality of what you’re buying and selling.
As long as everybody’s putting the information in SapphireOne correctly, then you know where to find it. If you don’t put things in the computer, you don’t know that it’s there. A little bit of that still happens with the staff manually inputting it. And that’s our biggest issue is just getting people to be 100% compliant.