10 Stocktaking Procedures to make your EOFY Obligations Stress-Free
June 28, 2019 12:50 pm | by John Adams
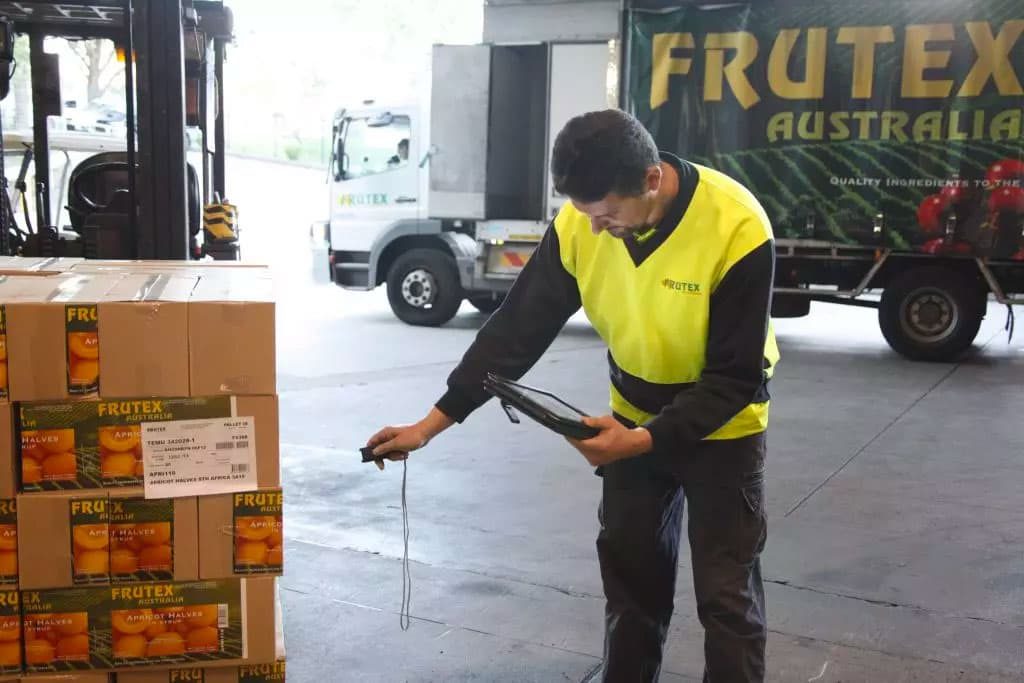
Its’ that time of the year again with the Australian Taxation Office requiring businesses that buy or sell stock to conduct a stocktake. This involves reconciling your physical stock with what’s listed in your inventory records. This can be a mammoth task but helps you make informed decisions, identify issues in stock management and processes. The right stocktaking procedures are the building blocks to a successful one.
How to make your stocktaking procedure as pain-free as possible?
1. Prepare and then prepare some more
Roster on extra staff to ensure the process is more efficient and runs smoothly. Make sure you have sufficient supplies such as barcode scanners, pens, clipboards, calculators, mobile devices, coffee, tea and water. Print out extra stock lists and train staff on how you would like them to count. Ask them to dress comfortably, take regular breaks and provide food.
2. Pick a time outside of normal operating hours
Ideally this is as close to the end of the financial year as practical. If possible a non-business day, before or after hours otherwise it’s best to close down. This stops your inventory levels changing during the stocktake.
3. Identify what stock is to be counted and where it’s located
Tidy up your storerooms, warehouses, stores and label the inventory. Create a stock list outlining which location the stock is held, where in the location, and what there is to be counted. Group similar inventory items together.
4. Define how you’re counting it
Let your staff know which sections they’ll be counting and in what order. Have a clear system for how they should physically count your stock. It’s a good idea to have a group of 2 for each unit of stocker takers. One person to count the inventory and call out the amount, the second person to record this number and double check the first.
5. Count everything
Every inventory item needs to be physically counted. Do not assume the current stocktake is correct. This should be treated as a comprehensive, full stocktake to know exactly what inventory is on hand. Check boxes and items are labelled correctly, their condition, and other storage areas for random items. Don’t forget to incorporate and count for returns, laybys and items on reserve.
6. Update your stock records
After the stocktake, be prepared for stage two. Your physical count needs to be checked against your inventory and accounting records. If you encounter discrepancies take immediate action to find out why. Any discrepancies found will need to be rechecked. All stock lists need to be completed and gathered so your data entry staff can enter into your accounting system. Make sure once the stock lists are entered, they are marked clearly so no duplications occur.
7. Formulate a plan for slow-selling items, thief and spoilage
Think about reducing inventory, analyse slow-selling items and create a plan for optimising the amount of inventory stored in your warehouse. Brainstorm ideas with the data collected to increase security and reporting procedures for damaged and spoiled stock.
8. Use technology available to streamline the process
If you are not using barcode scanners it may be time to think about investing in them. The scanned data can be imported wirelessly and directly into your ERP system. Investing in an ERP system will minimise errors and increase speed by real-time updates of the stock as they are counted. Stock items can be found in particular locations on mobile devices through inventory management in the software. An ERP system eliminates the need of data entry staff and manual record taking.
9. Review procedures
When completed, review your stocktaking procedures and note any suggestions to further streamline actions and improve processes for the next count.
10. Think about scheduling more than once a year
To keep on top of inventory it is easier to schedule multiple stocktakes throughout the year. These can be smaller, partial stocktakes so they don’t disrupt business. Think about dividing by stock items, brands and locations so you have inventory control all year-round, not just once a year.
Click for more information regarding the latest release of SapphireOne ERP, CRM, DMS and Business Accounting Software Application. Alternatively, contact our office on (02) 8362 4500 or request a demo.
GS1 Barcoding and Sharing of Information Seamlessly with SapphireOne ERP
February 19, 2019 4:00 pm | by John Adams
GS1 barcoding is transforming how you share information, as communicating with your customers, partners and suppliers is a crucial part of business. Their barcoding identifies, captures and shares information smoothly. They saw the need for a common language as when there are different processes and systems, the sharing of straightforward information can become time-consuming and error-prone. When everyone uses the same standards, it’s easier to get things done. GS1 barcodes are trusted and based on global standards.
SapphireOne has partnered with GS1 enabling clients to become compliant to their standards. These standards ensure key processes run smoothly in some of the world’s biggest industries.
GS1 Barcoding Standards- How They Work with SapphireOne
Identification standards contains numbers which are used to identify anything from products to invoices and warehouses. They make it easier to identify, track and share data in your supply chain.
Data capture currently uses globally-recognised standards to represent identification numbers. These data carriers capture information efficiently and effectively, bridging the gap between physical objects and electronic data.
SapphireOne uses these standards to automate the sharing of transactional information such as purchase orders and dispatch advice. This in turns saves time and money. GS1 synchronises the data with SapphireOne to share your company’s master data (product and pricing information) with all trading partners in your supply chain.
SapphireOne helps combine different GS1 standards resulting in streamlining business processes such as traceability.
The Importance of Barcode Integrity
All over the world, manufacturers and retailers rely on the GS1 system. Each barcode is issued by an authorised agent and are unique, accurate, and based on current global standards. In Australia, their barcode numbers begin with the prefix 93.
If you buy barcode numbers from a re-seller you do so at your own risk. All GS1 barcoding numbers are legitimate when first created, as soon as a re-seller buys a number and on-sells it to you, that number is no longer managed by GS1. This means there is no guarantee that the number will remain unique – which can have significant consequences within the supply chain, particularly in labelling and track and trace.
If unauthorised barcode numbers are purchased, sellers can create confusion in the market and disrupt the functioning of supply chains in Australia and overseas. Businesses need to be aware. If you obtain barcode numbers from an unauthorised source, you may suffer losses. These losses can be from re-labelling or repackaging your products, or if your products are rejected by your retail customer.
Click for more information regarding improvements and features within the latest release of SapphireOne ERP, CRM, DMS and Business Accounting Software Application. Alternatively, contact our office on (02) 8362 4500 or request a demo.